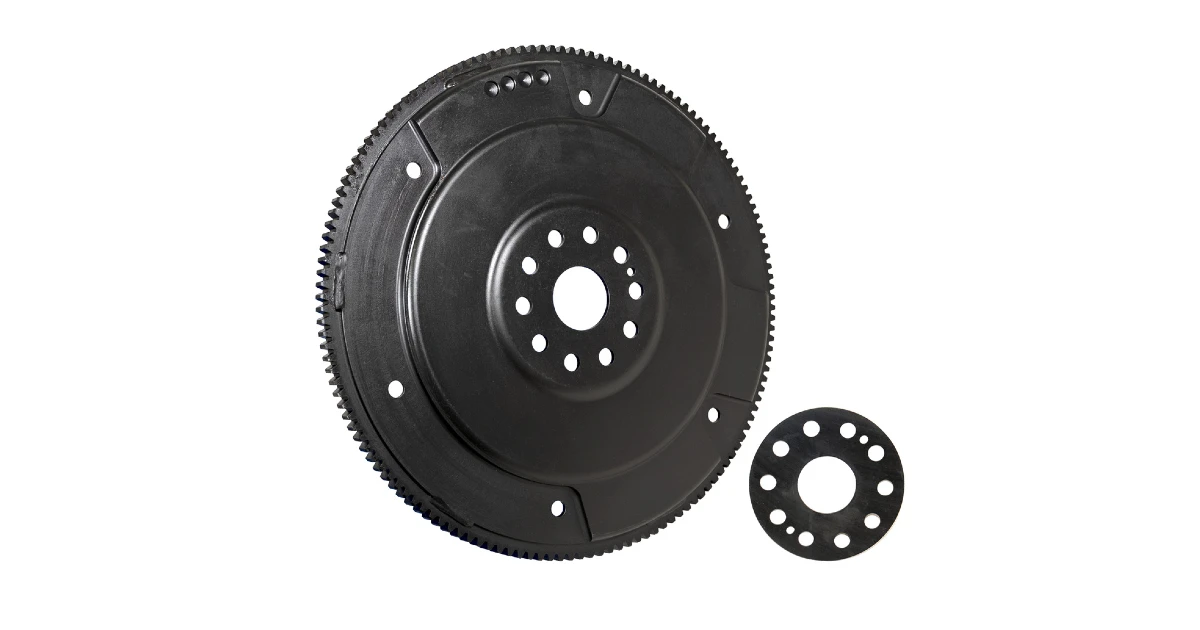
What is Black Oxidation?
Black oxidation is a surface treatment process that provides a black finish on metal parts. It forms a thin, adherent, and protective layer of black iron-oxide also known as magnetite (Fe3O4) on the surface of ferrous materials. This process enhances corrosion resistance and aesthetic appearance without affecting the dimensional integrity of the parts.
What does black oxide look like?
The black oxide process forms a very thin layer of black iron-oxide that does not significantly change surface finish. The surface finish after black oxidizing is basically a black version of the pre-blackening surface finish. If the component is polished to a mirror finish then black oxidized, it will then be a black mirror finish. If the component is a matte (e.g. sandblasted) finish then black oxidized, it will then be a black matte finish.
Advantages of Black Oxidation:
- Corrosion Resistance: The black oxide layer provides moderate corrosion resistance, especially when combined with oil or wax coatings, making it ideal for parts exposed to humidity and mild corrosive environments.
- Aesthetic Appeal: Black oxide imparts an attractive black finish that enhances the appearance of metal parts, suitable for both functional and decorative applications. Black Oxide can make your products more marketable.
- Dimensional Stability: The process does not significantly alter the dimensions of the treated parts, typically adding only about 5 to 10 millionths of an inch (0.000005” to 0.00001”) to the surface.
- Improved Lubricity: The porous nature of the oxide layer allows for better retention of lubricants, reducing friction and wear on moving parts.
- Uniform Finish: Black oxidation provides a uniform finish that can mask minor surface imperfections and improve the overall look of the parts.
Disadvantages of Black Oxidation:
- Limited Corrosion Protection: While it offers moderate corrosion resistance, black oxide is not suitable for highly corrosive environments unless additional coatings are applied.
- Surface Preparation: Proper surface preparation is required to achieve optimal results. Parts must be free from rust, oil, and other contaminants.
Surface Growth:
- Minimal Surface Growth: The black oxide layer adds only a very thin layer to the surface, typically around 5 to 10 millionths of an inch (0.000005” to 0.00001”), ensuring that there is no significant change in dimensions.
Surface Finish: Does Black Oxidation Affect Surface Finish?
- Enhancement of Appearance: Black oxidation provides a smooth and uniform black finish that can enhance the aesthetic appeal of parts.
- Surface Roughness: There is minimal change to surface roughness, making it suitable for parts that require precise surface finishes.
Stress Relieving: Does the Black Oxidation Process Relieve Stress?
- No Stress Relieving: The black oxidation process operates at lower temperatures (284-289°F) and does not relieve residual stresses in the material.
Tempering: Will Black Oxidation Temper My Parts?
- No Tempering Effect: The process temperature (<300°F) is not high enough to affect the tempering of hardened materials, maintaining the original mechanical properties of the parts.
Corrosion Resistance: How Does Black Oxidation Affect Corrosion Resistance?
- Enhanced Corrosion Resistance: The oxide layer provides a degree of corrosion protection, particularly when combined with post-treatment oils or waxes.
- Maintenance Required: Periodic reapplication of protective oils or waxes may be necessary to maintain optimal corrosion resistance.
Materials: What Materials Can Be Black Oxidized?
- Ferrous Metals: Black oxidation is suitable for various ferrous materials, including:
- Low and Medium Carbon Steels: Commonly treated to enhance appearance and corrosion resistance.
- Alloy Steels: Various alloy steels can also be black oxidized to improve surface properties.
- Tool Steels: Treated to enhance aesthetic appeal.
- Chemistry is Important. Our black oxide chemistry is not compatible with Cast Iron and Stainless Steels.
What is the Difference Between Hot and Cold Black Oxidation?
- Hot Black Oxidation: Involves immersing parts in a heated alkaline salt solution, providing a durable and uniform black finish. This is the process that Nitrera does.
- Cold Black Oxidation: Utilizes a room-temperature process with lower durability compared to hot black oxidation but is easier to apply. We do not do cold black oxide or cold bluing/cold blackening. Cold black oxide is applied at or near room temperature. It deposits a copper selenium compound onto the surface. This compound is not an acceptable substitute for hot black oxide as it does not look as nice and can tend to be very smutty (easily rubs off onto hands and clothes).
Re-Black Oxidizing: Can Parts Be Re-Black Oxidized?
Yes: Parts can be re-black oxidized to restore their appearance and protective properties, though proper surface preparation is essential.
Pre-Black Oxidizing Surface Condition Requirements:
Workpieces should be free of scale, rust, excessive oil/grease, machining chips in holes, and non-ferrous materials. Various cleaning methods are available, including aluminum oxide blasting, to prepare workpieces.
Applications of Black Oxidation:
- Fasteners: Improves corrosion resistance and appearance of bolts, nuts, and screws.
- Gears and Shafts: Enhances lubricity and corrosion resistance in mechanical components.
- Firearms: Provides an attractive black finish and corrosion protection for various firearm parts.
- Tools: Enhances the appearance of hand tools and cutting tools.
- Automotive Parts: Used on various automotive components to improve corrosion resistance and appearance.
- Machinery Components: Suitable for parts requiring improved lubricity and moderate corrosion resistance.
In summary, black oxidation is a versatile and cost-effective surface treatment process that enhances the appearance, corrosion resistance, and lubricity of ferrous metal parts. It is widely used across various industries for both functional and decorative applications.
Q vs QP vs QPQ Application Table
(Standard process)
Polish + Quench
Reduces Friction & Adhesion by up to 60%
Black Oxide (Quench) for Corrosion Resistance & Aesthetics.
Nitriding can increase RA up to ~32µin (0.8µm) total
QP restores RA to ~8-16µin (0.2-0.4µm)
RA can be restored to ~2µin (0.05µm) by hand polishing or other means.
Some material may be aesthetically affected by brown/red iron oxides (particularly stainless steels and cast iron)
Very high quality & consistent appearance from part to part & batch to batch.
Polishing removes brown oxides and other surface contamination & visible defects.
(Compared to Raw / un-Nitrided Material)
Martensitic stainless steels: Moderate increase
Nodular irons: Slight increase
Precipitation hardened stainless steels: Unchanged
Ferritic & Austenitic stainless steels: Decreased
Martensitic stainless steels: Same as Q
Nodular irons: Same as Q
Precipitation hardened stainless steels: Reduced compared to Q
Ferritic & Austenitic stainless steels: Further reduced compared to Q
Martensitic stainless steels: Likely better than Q
Nodular irons: Same as Q
Precipitation hardened stainless steels: Likely better than Q
Ferritic & Austenitic stainless steels: Significantly better than Q
Components with high-spec aesthetic requirements. E.g.: Firearms, tools, etc.
Everything else if the additional cost is worth it.
1 55-60HRC for Carbon Steels, 60-70HRC for Low-alloy Steels, 70HRC+ for Stainless Steels
2 Nitriding is not expected to increase surface roughness (RA) where the starting roughness is >32µin (0.8µm)
3 Up to ~400hr ASTM B117 salt spray test