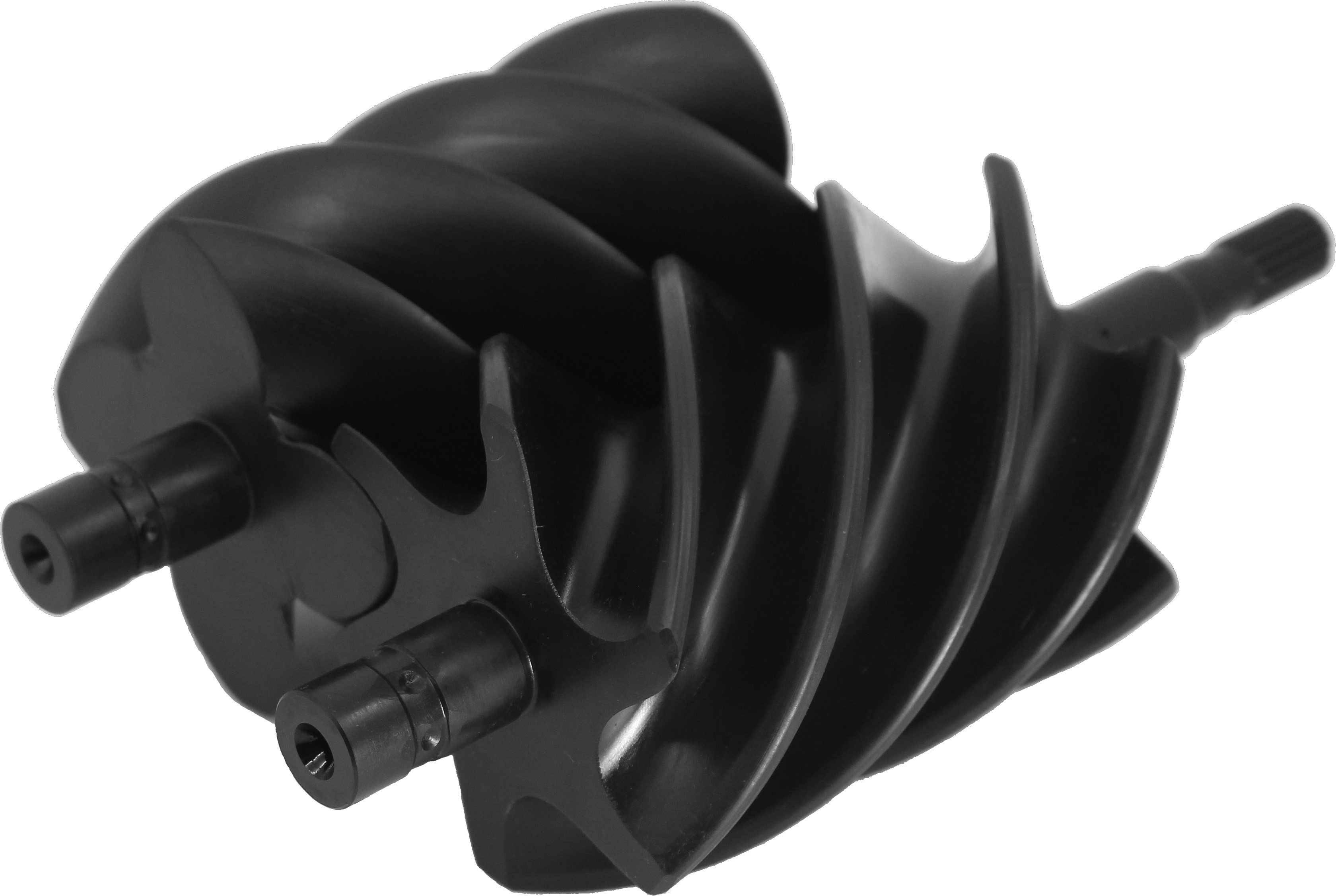
Introduction
Metallurgical advancements continue to revolutionize industries; one such development is Liquid Salt Bath Nitrocarburizing, or more commonly known as Liquid Nitriding. This process, crucial to fields of engineering and metallurgy, enhances the properties of metal components, notably improving their wear resistance fatigue strength and offering superior corrosion resistance.
From the automotive industry to aerospace and manufacturing, the application of Liquid Nitriding is widespread thanks to its beneficial impacts. But what makes it so vital? What outcomes does it render, and how does it bolster the quality and longevity of components?
In this article, we dive into the effectiveness of Liquid Nitriding, the critical role it plays in various sectors, and elucidate its intricate process. If you're keen to explore how this technique is supercharging metal parts and fortifying them against wear and tear, join us as we investigate the fascinating world of Liquid Nitriding.
Embracing Liquid Nitriding
Optimized Performance
Adopting Liquid Nitriding technology brings transformative enhancements to metal components. It ensures they are better-prepared to withstand high-stress applications and deliver optimized performance.
Extended Lifespan
By creating a hardened surface layer and enhancing the microstructure, this process can significantly increase the lifespan of mechanical parts. This longevity translates to reduced maintenance costs and sustained operational efficiency.
Enhanced Resistance
Liquid Nitriding is pivotal in improving the resistance of components to wear, corrosion, and fatigue. It especially benefits those exposed to harsh environments or high-stress situations.
Greater Reliability
A stronger, more resilient component translates to more reliable machinery and systems.
Through Liquid Nitriding, industries can reduce the risk of failure and ensure continuous, efficient operations.
Sustainable Innovation
The technology stands as a landmark of sustainable innovation in engineering. By enhancing component longevity and reducing the need for frequent replacements, it contributes to responsible resource utilization and waste reduction.
Competitive Advantage
With these benefits, industries embracing Liquid Nitriding technology stand to gain a significant competitive advantage. It's a smart strategy to produce high-quality, reliable products that outperform others in the market.
Process
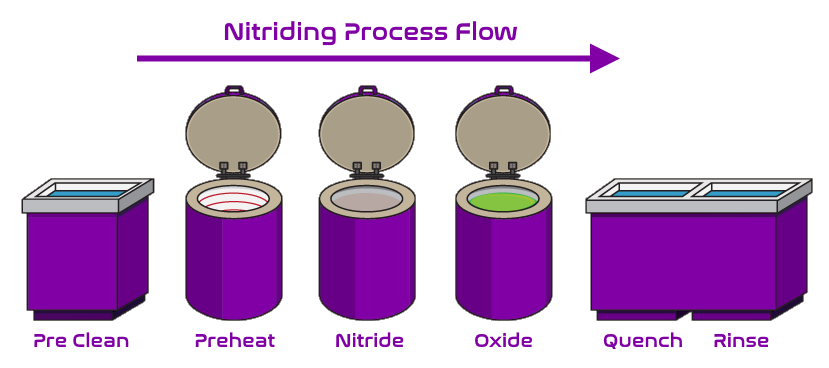
1. Pre Wash:
The process begins with a pre-wash step where the metal components are thoroughly cleaned to remove any contaminants, oils, or residues from their surfaces. This cleaning is essential to ensure proper nitrocarburizing and the formation of a uniform diffusion layer.
2. Preheat:
After cleaning, the components are preheated to a specific temperature range typically between 345°C to 455°C (650°F to 850°F). Preheating is essential in the formation of the iron-nitride compound layer (hardened surface), removing of any remaining moisture (safety), and to reduce the risk of thermal shock when the parts are immersed in the hot salt bath later in the process.
3. Nitride:
The core step of Liquid Salt Bath Nitrocarburizing is the nitriding phase. In this step, the preheated metal components are immersed in a specialized molten salt bath containing nitrogen-bearing compounds. The elevated temperature of the bath (usually around 568°C or 1055°F) facilitates the diffusion of nitrogen and carbon into the surface of the components. This creates a hardened layer rich in iron-nitride and carbon-nitride compounds, enhancing surface hardness and wear resistance. It also acts as a barrier to corrosion.
4. Oxide:
Following nitriding, the components are subjected to an oxidizing quench step (usually around 400°C to 455°C or (750°F to 850°F). Quenching helps to "freeze" the microstructure, locking in the desired hardness and improving the mechanical properties of the treated layer. Here the parts are immersed into a solution of black oxidizing salts. The goal is to form a thin, protective black oxide layer on the surface of the nitrided layer. This oxide layer further improves corrosion resistance, contributes to the overall durability of the treated components, and imparts pleasing aesthetics. This step also detoxifies the residual salts for environmental and worker safety reasons.
5. Quench:
After the nitriding and oxide formation steps, the parts are quenched. Quenching is often done in water (water quench), but can also be done in air (air quench) for certain parts that may benefit from a slower change in temperature.
6. Rinse:
The final step involves rinsing the components to remove any residual salts. Proper rinsing ensures that no residues remain on the treated parts. After rinsing, the components may undergo further cleaning or drying processes before being deemed ready for use or additional finishing steps.
These six process steps work together to transform the surface properties of metal components, making them harder, more wear-resistant, corrosion-resistant, and fatigue-resistant. Liquid Salt Bath Nitrocarburizing is widely utilized in various industries to enhance the performance and longevity of critical metal parts and components.
Conclusion
Liquid Nitriding stands as an essential, transformative process in modern metallurgy and engineering. The significant improvements it brings to the wear resistance, corrosion resistance, and fatigue strength of metal components provide manufacturers a competitive edge.
Recognizing its potential is highly crucial for the manufacturing industry's relentless pursuit of quality, durability, and cost-effectiveness. Therefore, it's time to take action by embracing and investing in this cutting-edge surface treatment technology.
Want to learn more about how you can harness the benefits of Liquid Nitriding? As industry experts in this field, Nitrera Technologies is equipped to guide you through the process.
Servicing all United States and Canada, particularly in the West, we offer top-tier Liquid Nitriding services. Give us a call at (778) 298-2217 or contact us on our website, and let's make your metal components more efficient, durable, and cost-effective with Liquid Nitriding.
Q vs QP vs QPQ Application Table
(Standard process)
Polish + Quench
Reduces Friction & Adhesion by up to 60%
Black Oxide (Quench) for Corrosion Resistance & Aesthetics.
Nitriding can increase RA up to ~32µin (0.8µm) total
QP restores RA to ~8-16µin (0.2-0.4µm)
RA can be restored to ~2µin (0.05µm) by hand polishing or other means.
Some material may be aesthetically affected by brown/red iron oxides (particularly stainless steels and cast iron)
Very high quality & consistent appearance from part to part & batch to batch.
Polishing removes brown oxides and other surface contamination & visible defects.
(Compared to Raw / un-Nitrided Material)
Martensitic stainless steels: Moderate increase
Nodular irons: Slight increase
Precipitation hardened stainless steels: Unchanged
Ferritic & Austenitic stainless steels: Decreased
Martensitic stainless steels: Same as Q
Nodular irons: Same as Q
Precipitation hardened stainless steels: Reduced compared to Q
Ferritic & Austenitic stainless steels: Further reduced compared to Q
Martensitic stainless steels: Likely better than Q
Nodular irons: Same as Q
Precipitation hardened stainless steels: Likely better than Q
Ferritic & Austenitic stainless steels: Significantly better than Q
Components with high-spec aesthetic requirements. E.g.: Firearms, tools, etc.
Everything else if the additional cost is worth it.
1 55-60HRC for Carbon Steels, 60-70HRC for Low-alloy Steels, 70HRC+ for Stainless Steels
2 Nitriding is not expected to increase surface roughness (RA) where the starting roughness is >32µin (0.8µm)
3 Up to ~400hr ASTM B117 salt spray test