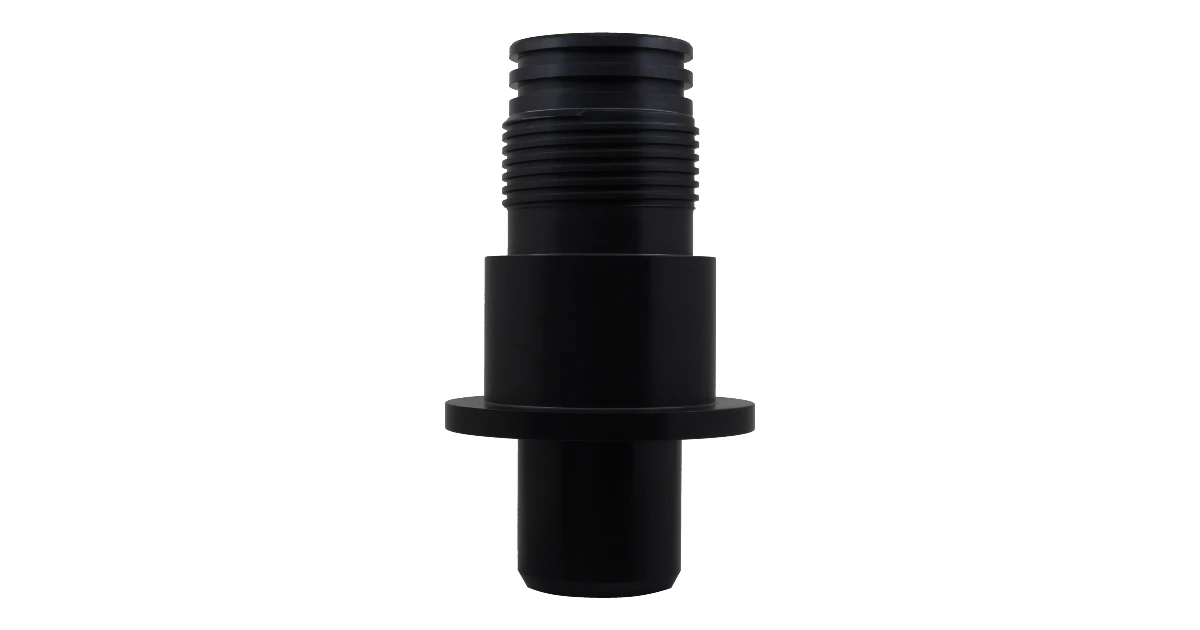
Compatible Materials & Components
Nitrocarburizing is primarily designed for ferrous materials, particularly various types of steel and iron alloys. These materials are highly compatible with the nitrocarburizing process due to their ability to readily diffuse nitrogen and carbon at the elevated temperatures used in the process. Here are some materials that are generally compatible with nitrocarburizing:
- Low and Medium Carbon Steels: These are among the most common materials processed using nitrocarburizing. Examples include AISI 1018, 1020, and 1045 steels.
- Alloy Steels: Various alloy steels, including those with higher levels of carbon and additional alloying elements, can undergo nitrocarburizing. Examples include AISI 4140, 4130, 4145, 4340, 4320, and 8620.
- Tool Steels: Tool steels are often treated with nitrocarburizing to enhance their wear resistance and durability. Examples include A1, A2, O1, O2, H13 and D2 tool steels.
- Cast Iron: Gray cast iron and ductile cast iron are compatible with nitrocarburizing, with the process providing increased wear resistance and improved surface hardness. E.g. Ductile Iron, Grey Iron, Nodular Iron.
- Stainless Steels: Stainless steel alloys can be nitrocarburized to improve wear & galling resistance. Common examples include 303, 304, 316, 416, 17-4 PH and 15-5 PH stainless steels.
- Sintered Materials: Powder metallurgy components, such as those made from sintered or 3D printed steel, can undergo nitrocarburizing to improve surface properties.
- Nickel-Based Alloys: Some nickel alloys can also be nitrocarburizing including Inconel 718
- Automotive and Machinery Components: Various components used in the automotive and machinery industries, including gears, crankshafts, and camshafts, are often nitrocarburized for improved performance and longevity.
- Firearms Components: Gun barrels and other firearm components such as actions, bolts, and magazines are often nitrocarburized to enhance wear resistance and corrosion resistance.
- Agricultural and Construction Equipment Parts: Components used in heavy machinery and equipment benefit from nitrocarburizing to withstand harsh working conditions.
- Aerospace Components: Certain aerospace components made from compatible ferrous materials can undergo nitrocarburizing to enhance their performance and durability.
Incompatible Materials & Components
Nitrocarburizing is primarily designed for ferrous materials, such as steel and iron alloys. It may not be suitable for non-ferrous materials and materials with certain characteristics or coatings. Here are some materials and material conditions that are generally considered incompatible with nitrocarburizing:
- Non-Ferrous Materials: Nitrocarburizing is not suitable for non-ferrous materials like aluminum, copper, brass, or bronze, as these materials do not readily diffuse nitrogen and carbon in the nitrocarburizing process.
- Components with Sensitive Heat Treatments: Components that have undergone specific heat treatments, especially those that involve sensitive temperature ranges, may not be compatible, as the nitrocarburizing process involves elevated temperatures.
- Components with Non-Metallic Coatings: Components with non-metallic coatings like paint, plastic, or rubber may not be compatible, as the coatings can deteriorate or produce undesirable reactions in the salt bath. We can often remove these coatings for you by sand blasting.
- Components with Thin Wall Sections: Extremely thin-walled components may not be suitable for nitrocarburizing, as the process could lead to distortion or warping. We have successfully nitrided cross-sections as thin as 0.002” with reduced soak time.
- Components with Platings or Surface Treatments: Components with pre-existing platings or surface treatments may require special consideration, as these layers may need to be removed before nitrocarburizing. Platings can often be stripped by “pickling” in acid at a plating shop, then nitrided.
Recommendations
We are often asked to recommend material for an application. This is a very complicated subject, but without getting too deep into material science, there are some general guidelines and common recommendations.
Generally, any iron-based material that meets the required mechanical properties of the application (e.g. strength), and whose prior heat treatment (if any) can tolerate the nitrocarburizing process temperature, is likely a good candidate for nitrocarburizing if you are looking to add any or all of the following: Surface hardness, wear resistance, galling resistance, corrosion resistance, and black finish. One exception however is stainless steels. Depending on the grade, stainless steels corrosion resistance may be reduced.
Stainless steel corrosion resistance may be reduced or improved depending on the type of stainless steel i.e. Martensitic, Ferritic or Austenitic. Stainless steel corrosion resistance also depends on how we perform the nitrocarburizing process (Q vs QP vs QPQ). Please see the corrosion resistance section of our Q vs QP vs QPQ article here.
Consider the prior heat treatment of a material finished component, or combining nitrocarburizing with a conventional treatment such as quench & temper, induction hardening, or carburizing.
The effect that nitriding will have on Induction hardening, laser hardening, and flame hardening, is similar to the effect on quench & temper. In this regard, think of nitriding as a tempering process. If the material is 4140 and the induction/flame/laser hardened case is 50HRC and the core is 30HRC, then nitriding will not soften the core but will soften the induction/flame/laser hardened case to about 36HRC.
Q vs QP vs QPQ Application Table
(Standard process)
Polish + Quench
Reduces Friction & Adhesion by up to 60%
Black Oxide (Quench) for Corrosion Resistance & Aesthetics.
Nitriding can increase RA up to ~32µin (0.8µm) total
QP restores RA to ~8-16µin (0.2-0.4µm)
RA can be restored to ~2µin (0.05µm) by hand polishing or other means.
Some material may be aesthetically affected by brown/red iron oxides (particularly stainless steels and cast iron)
Very high quality & consistent appearance from part to part & batch to batch.
Polishing removes brown oxides and other surface contamination & visible defects.
(Compared to Raw / un-Nitrided Material)
Martensitic stainless steels: Moderate increase
Nodular irons: Slight increase
Precipitation hardened stainless steels: Unchanged
Ferritic & Austenitic stainless steels: Decreased
Martensitic stainless steels: Same as Q
Nodular irons: Same as Q
Precipitation hardened stainless steels: Reduced compared to Q
Ferritic & Austenitic stainless steels: Further reduced compared to Q
Martensitic stainless steels: Likely better than Q
Nodular irons: Same as Q
Precipitation hardened stainless steels: Likely better than Q
Ferritic & Austenitic stainless steels: Significantly better than Q
Components with high-spec aesthetic requirements. E.g.: Firearms, tools, etc.
Everything else if the additional cost is worth it.
1 55-60HRC for Carbon Steels, 60-70HRC for Low-alloy Steels, 70HRC+ for Stainless Steels
2 Nitriding is not expected to increase surface roughness (RA) where the starting roughness is >32µin (0.8µm)
3 Up to ~400hr ASTM B117 salt spray test