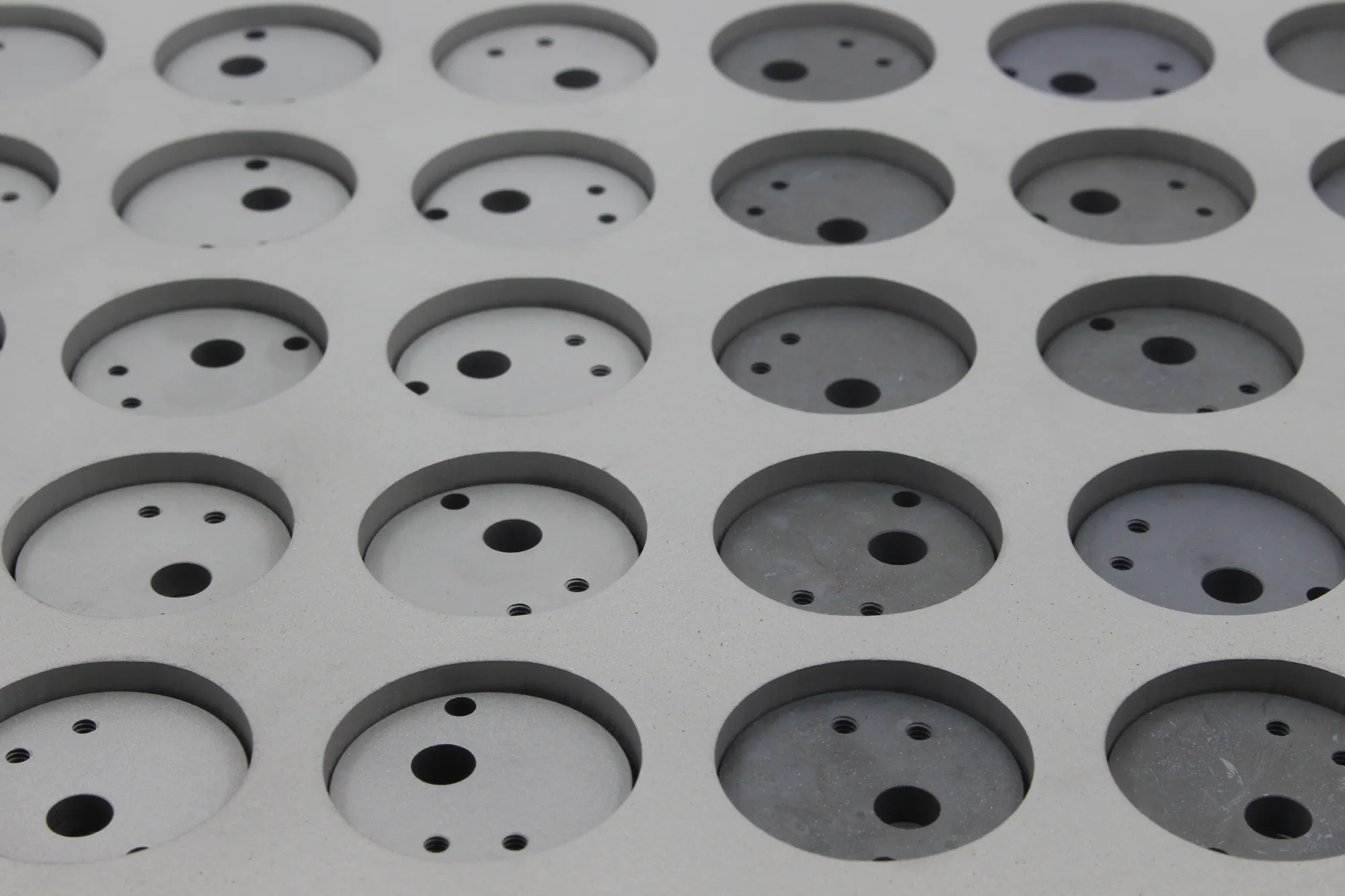
What is Surface Finishing?
Surface finishing is the process of treating the surface of a material to ensure it is clean and/or smooth (or just of the desired “finish/appearance”) often in preparation for subsequent processes such as coating, painting, or other finishing. Proper surface finishing enhances adhesion of coatings, appearance, and the overall quality of the final product.
Why is Surface Finishing Important?
∙ Surface Cleanliness: Removes contaminants like oils, rust, and scale that can interfere with finishing processes.
∙ Nitriding: Allows for homogeneous diffusion of nitrogen which is critical for iron-nitride compound layer formation, depth of case hardening, and corrosion resistance.
∙ Black Oxidizing: Allows for homogeneous conversion of surface iron to black iron-oxide (Fe3O4), which is critical for aesthetics and corrosion resistance.
∙ Adhesion Improvement: Properly finished surfaces ensure better adhesion of coatings, paints, and finishes. We offer our surface finishing service as a surface prep for other outside processed that we do not offer such as powder coating, painting, etc.
∙ Aesthetic Enhancement: Creates a uniform surface that improves the appearance of the final product. Sometimes a product just needs to be glass bead polished or aluminum oxide blasted to restore its original function and appearance.
∙ Corrosion Resistance: Prepares the surface for treatments that enhance corrosion resistance.
Surface Finishing Methods at Nitrera:
- Aluminum Oxide Sand Blasting
- Glass Bead Polishing
- Acid Etching
- Prewashing
Aluminum Oxide Sand Blasting
What is Aluminum Oxide Sand Blasting? Aluminum oxide sand blasting is a method of mechanical surface finishing that involves propelling fine crystalline particles of aluminum oxide (Al2O3) at high speed onto a surface. This process cleans, smooths, (and roughens) surfaces to improve reactivity and/or adhesion for coatings and finishes. Sometimes aluminum oxides utilization is more about the desirable matte finish than the cleaning.
Advantages:
∙ Effective Cleaning: Removes rust, scale, paint, and other contaminants effectively.
∙ Aesthetics: Aluminum Oxide imparts a matte finish that is pleasing to the eye.
∙ Surface Roughening: Creates an ideal texture for improved subsequent processes such as coatings.
∙ Versatility: Suitable for a wide range of materials, including metals.
∙ Dimensional Stability: Does not remove a significant amount of material.
Disadvantages:
∙ Dust Generation: Generates dust that requires proper evacuation, filtration, ventilation and protective equipment.
What Kind of Aluminum Oxide Blasting Do You Offer?
We stock aluminum oxide in 100-120 grit. The work is performed in 2x4 foot clamp shell style sand blasting cabinets. All work is done by hand.
Can You Selective Mask Off Areas?
Yes, we have a large variety of rubber plugs for holes & bores. Outside features can be masked off with tape.
Glass Bead Polishing
What is Glass Bead Polishing?
Glass bead polishing another type of mechanical cleaning involves blasting the surface with fine glass beads (SiO2 / silicon-dioxide) to clean and smooth it. This method is used to create a uniform, satin finish and to prepare surfaces for subsequent treatments. Sometimes aluminum oxides utilization is more about the desirable satin finish than the cleaning. For some products we aluminum oxide to remove heavy scale, then glass bead to apply a satin finish, depending on customer requirements. Mostly we glass bead Nitrided parts after nitriding to restore the original machined finish and enhance appearance in a process known as QP. See our Article on Q vs QP vs QPQ.
Advantages:
∙ Smooth Finish: Provides a smooth, uniform satin finish.
∙ Aesthetics: Glass Bead imparts a satin finish that is pleasing to the eye.
∙ Non-Abrasive: Gentle on the surface, making it suitable for delicate or nitrided parts.
∙ Improved Appearance: Enhances the aesthetic appeal of the surface.
∙ Dimensional Stability: Does not remove a significant amount of material.
Disadvantages:
∙ Limited Material Removal: Less effective at removing heavy rust or scale compared to more abrasive methods.
What Kind of Glass Bead Polishing Do You Offer?
We stock glass beads in mil spec #13 which is a particle diameter of 0.0017-0.0035” (we can stock other sizes upon request). The work is performed in 2x4 foot clamp shell style sand blasting cabinets. All work is done by hand.
Can You Selectively Mask Off Areas?
Yes, we have a large variety of rubber plugs for holes & bores. Outside features can be masked off with tape.
Acid Etching
What is Acid Etching?
Acid etching is a type of chemical cleaning which involves submerging parts into a controlled chemical solution to a surface to clean, remove oxides, and remove plating’s such as chrome & zinc. We usually use hydrochloric acid (HCl) but also stock sulphuric acid (H2SO4).
We use Acid Etching to:
∙ Strip chrome, zinc or other plating’s from parts that one desires to nitride or black oxide, such as firearms, golf club heads, and more. Since nitriding or black oxidizing only work if they can react with iron, plates must be removed.
∙ Strip chrome, zinc or other plating’s from fastener and other devices that we wish to use for fixturing parts for processing in our nitride or black oxide baths.
∙ Rework black oxidized products that need to be retreated but cannot be surface prepped with aluminum oxide or glass bead owing to surface finish requirements.
Advantages:
∙ Effective Cleaning: Removes oxides, contaminants, and impurities from the surface.
∙ Enhanced Adhesion: Creates a microscopically rough surface that enhances the adhesion of coatings.
Disadvantages:
∙ Handling Hazards: Involves hazardous chemicals that require careful handling and disposal.
∙ Surface Damage: Can cause damage if the concentration or exposure time is not properly controlled.
Prewashing
What is Prewashing?
Prewashing is an alkaline cleaning process that removes soils such as oils, grease, dirt, and other contaminants from a surface before further treatment. It is often the first step in surface finishing. All parts (except those that have been aluminum oxide blasted, glass bead polished, or acid etched) are prewashed before being nitrided or black oxidized. Even if a batch has only a few parts that were not surface prepped by mechanical or chemical means, it will get prewashed. This method of cleaning is applied by immersion. the parts to be cleaned are immersed in the solution and allowed to soak. As the alkaline cleaner acts on the parts, convection currents (due to heating or mechanical agitation) help to lift and remove soils from the metal surface.
Advantages:
∙ Thorough Cleaning: Ensures that surfaces are free of contaminants that can interfere with subsequent processes.
∙ Improved Process Efficiency: Prepares the surface for more effective and efficient subsequent treatments.
∙ Downstream Benefits: Most dirty parts can more than likely tolerate being nitrided without a prewash, but if that contamination is allowed to into the nitriding salt bath, it increases the rate of sludge buildup in the nitriding bath and causes increased maintenance.
Which Surface Finishing Method Does Nitrera Use on My Parts?
The choice of surface finishing method depends on several factors, including the material of the workpiece, prior heat treatment (if any), the type of contaminants, the desired surface finish (drawing review), and the subsequent treatment or coating process. Here are some general guidelines:
∙ Heavy Rust and Scale & Oxidation Removal: Aluminum oxide sand blasting.
∙ Very Light & Gentle Cleaning: Glass bead polishing.
∙ Plating Removal: Acid etching.
∙ General Cleaning: Prewashing.
In summary, surface finishing is a crucial step in ensuring the quality and performance of nitriding, black oxidizing, and other coatings & finishes. By selecting the appropriate method and following best practices, we achieve optimal results for your specific application.
Q vs QP vs QPQ Application Table
(Standard process)
Polish + Quench
Reduces Friction & Adhesion by up to 60%
Black Oxide (Quench) for Corrosion Resistance & Aesthetics.
Nitriding can increase RA up to ~32µin (0.8µm) total
QP restores RA to ~8-16µin (0.2-0.4µm)
RA can be restored to ~2µin (0.05µm) by hand polishing or other means.
Some material may be aesthetically affected by brown/red iron oxides (particularly stainless steels and cast iron)
Very high quality & consistent appearance from part to part & batch to batch.
Polishing removes brown oxides and other surface contamination & visible defects.
(Compared to Raw / un-Nitrided Material)
Martensitic stainless steels: Moderate increase
Nodular irons: Slight increase
Precipitation hardened stainless steels: Unchanged
Ferritic & Austenitic stainless steels: Decreased
Martensitic stainless steels: Same as Q
Nodular irons: Same as Q
Precipitation hardened stainless steels: Reduced compared to Q
Ferritic & Austenitic stainless steels: Further reduced compared to Q
Martensitic stainless steels: Likely better than Q
Nodular irons: Same as Q
Precipitation hardened stainless steels: Likely better than Q
Ferritic & Austenitic stainless steels: Significantly better than Q
Components with high-spec aesthetic requirements. E.g.: Firearms, tools, etc.
Everything else if the additional cost is worth it.
1 55-60HRC for Carbon Steels, 60-70HRC for Low-alloy Steels, 70HRC+ for Stainless Steels
2 Nitriding is not expected to increase surface roughness (RA) where the starting roughness is >32µin (0.8µm)
3 Up to ~400hr ASTM B117 salt spray test