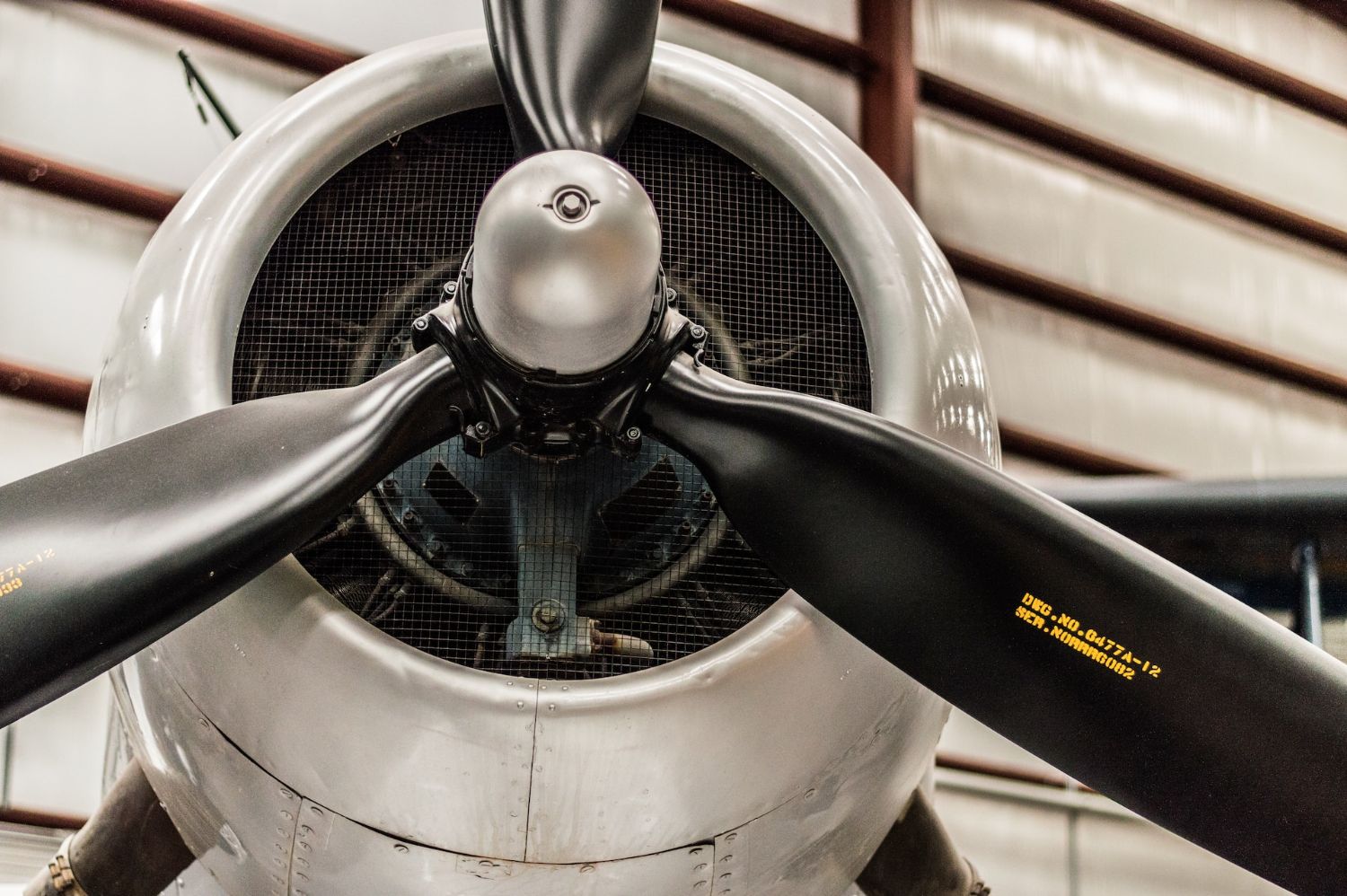
Introduction
In the demanding world of aerospace and aviation, the materials and processes used in manufacturing and maintaining aircraft components are critical. As a metallurgical engineer, I have observed firsthand the transformative impact of Liquid Nitriding on the aerospace and aviation industry. This article aims to explore the applications, benefits, and technical nuances of Liquid Nitriding in this high-stakes field.
Understanding Liquid Nitriding
Liquid Nitriding, a thermochemical process, involves immersing metal parts in a molten salt bath at temperatures typically between 500°C and 600°C. This process enriches the surface of the metal with nitrogen and carbon, resulting in a hardened surface layer.
Key Characteristics
- Enhanced Surface Hardness: The process significantly increases the surface hardness of the treated materials, making them more resistant to wear.
- Improved Fatigue Strength: Treated components demonstrate greater resistance to cyclic stress.
- Corrosion Resistance: The nitriding process offers enhanced corrosion resistance, crucial for aircraft components exposed to various environmental conditions.
Liquid Nitriding in Aerospace & Aviation
The aerospace industry demands materials that can withstand extreme conditions while maintaining structural integrity and safety. Here, Liquid Nitriding finds its significance.
Turbine Blades and Engine Components
The efficiency and safety of aircraft engines rely heavily on the durability of their components. Liquid Nitriding is used to treat turbine blades, enhancing their resistance to high temperatures and reducing the risk of failure due to thermal fatigue.
Landing Gear
The landing gear of aircraft undergoes immense stress during takeoff and landing. Nitriding these components improves their wear resistance, ensuring a longer service life and reducing maintenance frequency.
Fasteners and Bearings
Aircraft fasteners and bearings, integral to the structural integrity, benefit from the wear resistance and strength provided by Liquid Nitriding, ensuring reliable performance over extended periods.
Technical Insights
Liquid Nitriding, while offering significant benefits, requires precise control and expertise.
Process Parameters
- Temperature Control: Precise temperature control is crucial to achieving the desired case depth and hardness.
- Time in Bath: The duration of immersion affects the depth of nitrided layer, which is critical for achieving the desired properties.
- Salt Bath Composition: The composition of the salt bath must be carefully managed to ensure uniformity in the nitriding process.
Quality Control and Testing
Post-treatment testing is essential to ensure the components meet the stringent standards of the aerospace industry. This includes hardness testing, microstructure analysis, and corrosion resistance checks.
Advantages Over Alternative Methods
While there are other surface hardening techniques, Liquid Nitriding offers distinct advantages in aerospace applications.
Comparing with Gas Nitriding
- Uniform Treatment: Liquid Nitriding ensures more uniform treatment of complex shapes, a common characteristic of aerospace components.
- Shorter Cycle Time: The process is generally faster than gas nitriding, leading to increased efficiency in production.
Environmental Considerations
Liquid Nitriding, compared to some other treatments, can be more environmentally friendly, with advancements in salt bath recycling and waste management.
Future Perspectives
The future of Liquid Nitriding in aerospace and aviation looks promising, with ongoing research and development focusing on optimizing the process and expanding its applications.
Innovations in Process Control
Advancements in process control and monitoring are expected to further enhance the precision and efficiency of Liquid Nitriding, making it more adaptable to a variety of aerospace materials and components.
Emerging Applications
Research into the use of Liquid Nitriding for newer aerospace materials, including advanced alloys and composites, is opening new frontiers in this field.
Conclusion
As we continue to push the boundaries of aerospace engineering, the role of advanced surface treatments like Liquid Nitriding becomes increasingly vital. Its ability to significantly improve wear resistance, fatigue strength, and corrosion resistance makes it an indispensable process in the aerospace and aviation industry. The ongoing advancements in this field promise to further enhance the safety, efficiency, and performance of aerospace components, ensuring that Liquid Nitriding remains at the forefront of metallurgical innovation in aviation.