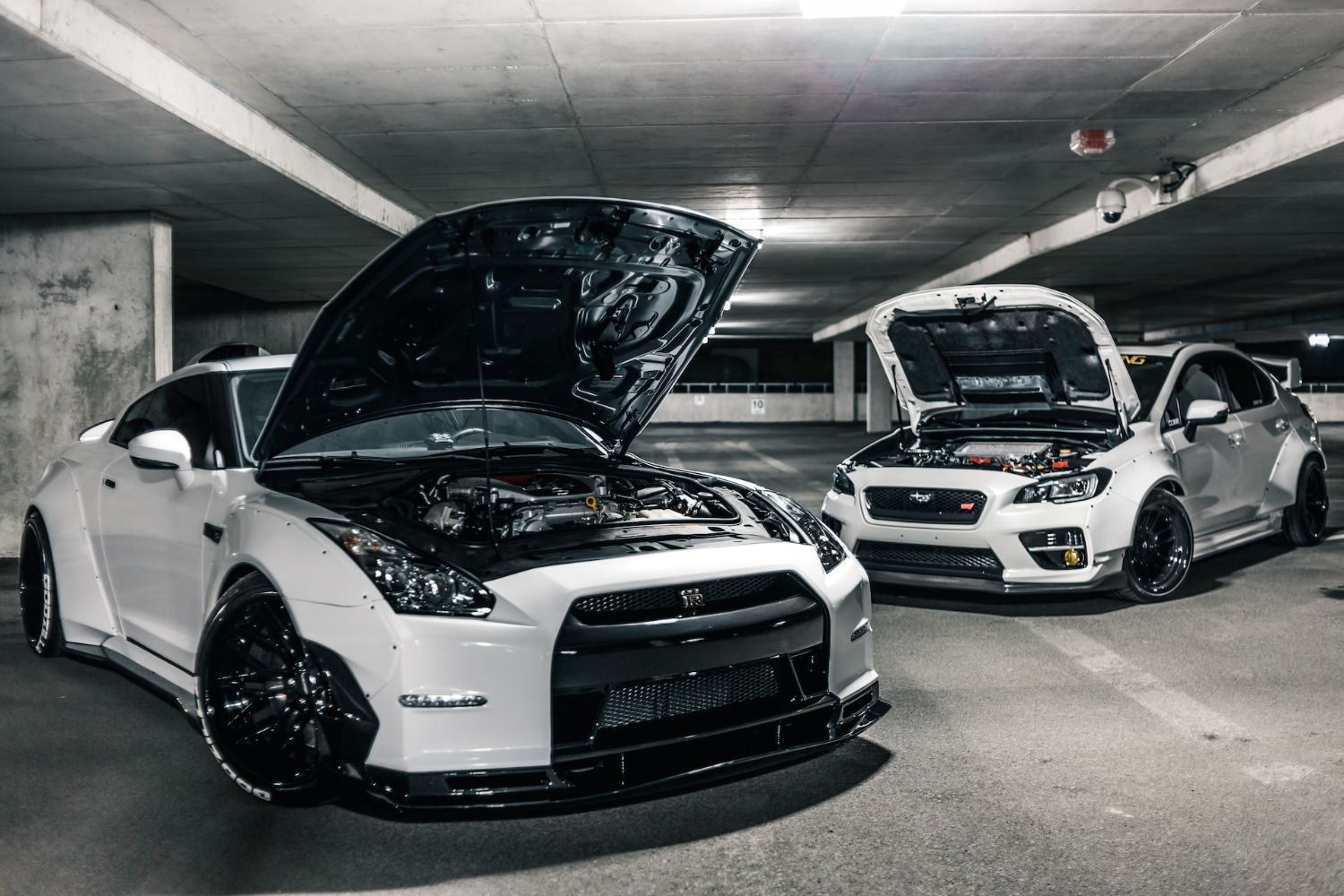
The Need for Advanced Material Treatments in Automotive Engineering
The automotive industry constantly seeks innovative solutions to improve the performance, efficiency, and longevity of vehicle components. With the increasing demand for high-performance vehicles and the ongoing shift towards electric vehicles, the need for advanced material treatments like liquid nitriding has never been more critical.
What is Liquid Nitriding?
Liquid nitriding, also known as salt bath nitriding, is a thermochemical process that introduces nitrogen into the surface layer of steel and other alloys. This treatment forms a hard, wear-resistant layer, known as the nitride layer, which significantly improves the material's properties.
The Process of Liquid Nitriding
The process involves submerging the metal components into a molten salt bath that contains nitrogen-donating chemicals. The temperature of this bath is typically between 495°C to 565°C (930°F to 1050°F). This high temperature allows for the diffusion of nitrogen and, to a lesser extent, carbon into the surface of the steel, creating a toughened layer.
Benefits of Liquid Nitriding in Automotive Applications
Enhanced Wear Resistance
One of the primary advantages of liquid nitriding is the remarkable improvement in wear resistance. This is particularly beneficial for automotive components such as gears, crankshafts, and camshafts, which are subject to constant friction and wear.
Improved Fatigue Strength
Fatigue failure is a common issue in automotive parts subjected to cyclic stress. Liquid nitriding significantly increases the fatigue strength of these components, thereby enhancing their ability to withstand repeated stress without failing.
Superior Corrosion Resistance
Corrosion can drastically reduce the life of automotive parts. Liquid nitriding imparts a high level of corrosion resistance, making it an ideal treatment for components exposed to harsh environmental conditions.
Increased Surface Hardness
The process results in a surface that is substantially harder than the untreated metal. This increased hardness translates to improved performance and a longer lifespan for automotive components.
Applications in the Automotive Industry
Liquid nitriding is utilized in various automotive components, some of which include:
- Engine Components: Parts like valves, piston rings, and camshafts benefit greatly from the enhanced wear resistance and reduced friction provided by liquid nitriding.
- Transmission Systems: Gears and shafts in transmission systems, treated with liquid nitriding, exhibit increased resistance to wear and fatigue.
- Suspension Systems: Components within the suspension system, such as springs and shock absorber rods, gain improved resilience and longevity from the nitriding process.
Environmental Considerations
In today's environmentally conscious world, it's essential to consider the ecological impact of industrial processes. Liquid nitriding, when performed with modern methods, can be environmentally friendly. Advances in the process have led to the development of eco-friendly salt baths and waste management techniques that minimize environmental impact.
The Future of Liquid Nitriding in Automotive Engineering
As the automotive industry continues to evolve, the role of advanced material treatments like liquid nitriding becomes increasingly significant. With the ongoing push towards lightweight materials and the need for components that can withstand more rigorous operational demands, liquid nitriding is poised to play a crucial role in future automotive developments.
Conclusion
Liquid nitriding is more than just a surface treatment; it's a gateway to new levels of performance and durability in the automotive industry. As engineers, embracing these advanced processes is essential for driving innovation and meeting the ever-increasing demands of modern automotive design and manufacturing.
The application of liquid nitriding in the automotive industry exemplifies the remarkable synergy between materials science and engineering. By enhancing the fundamental properties of metal components, we are not only improving the performance and efficiency of vehicles but also contributing to a more sustainable future in automotive manufacturing.