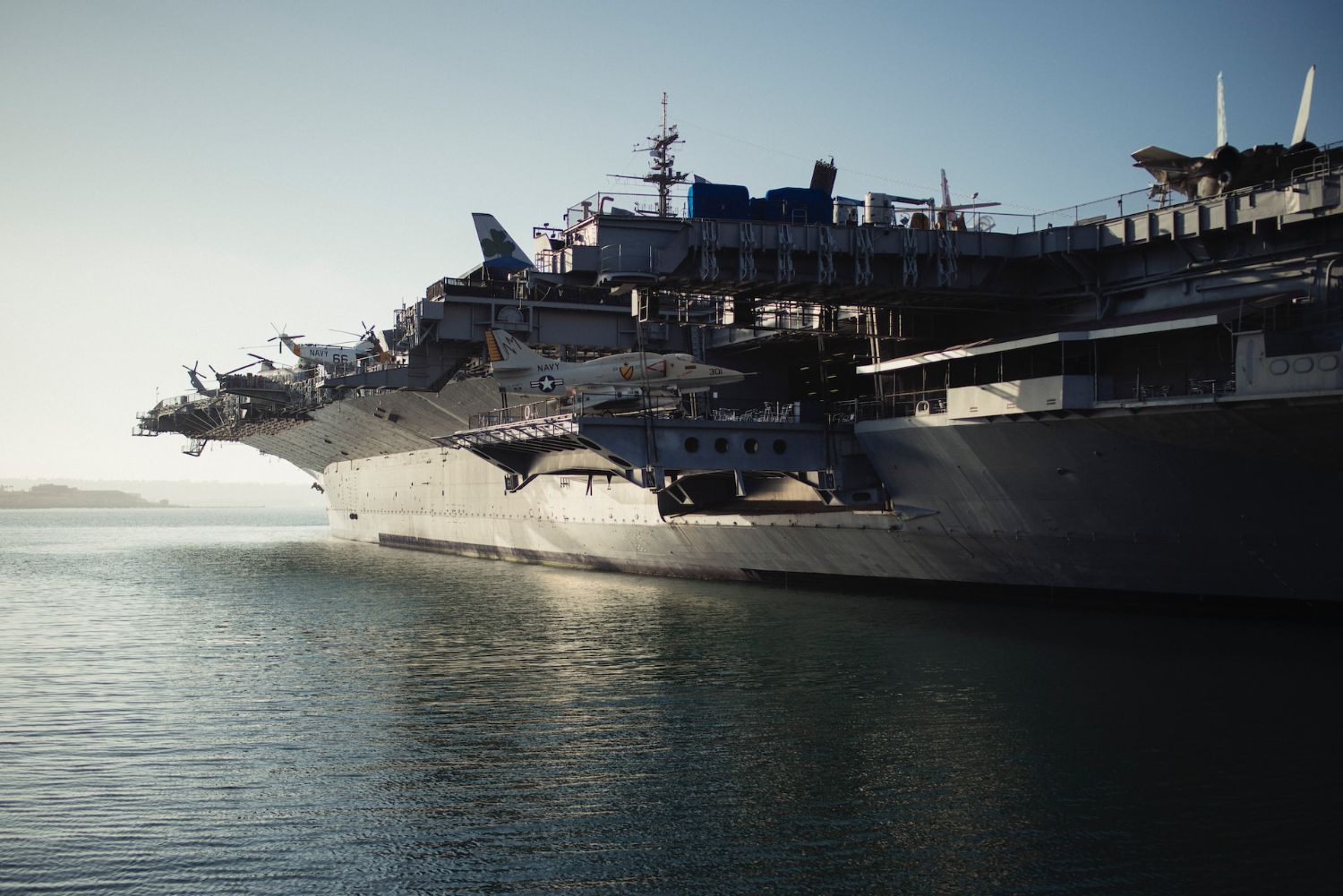
Introduction
The defense and military industry is an arena where material performance can mean the difference between success and failure, safety and risk. As a metallurgical engineer, I've observed how advancements in materials engineering, particularly liquid nitriding, have dramatically enhanced the durability and functionality of military equipment. This article delves into the world of liquid nitriding and its pivotal role in the defense sector.
Understanding Liquid Nitriding
The Process Explained
Liquid nitriding, a thermochemical treatment, involves immersing metal components in a nitrogen-rich salt bath at high temperatures. This process enriches the surface of the metal with nitrogen, creating a hardened layer that significantly improves wear resistance, fatigue strength, and corrosion resistance.
Material Transformations
Metals treated with liquid nitriding exhibit remarkable improvements in surface hardness and resistance to harsh environmental conditions. This transformation is crucial for military applications where materials are frequently subjected to extreme stress and corrosive elements.
Applications in Defense & Military
Armored Vehicles Enhancement
Liquid nitriding is extensively used to treat parts of armored vehicles, including ballistic protection components. This treatment enhances their resistance to impact and abrasion, ensuring the longevity and reliability of these critical assets.
Weaponry and Ammunition
From small arms to large artillery, liquid nitriding provides an extra layer of durability. Barrels, breech mechanisms, and other firearm components benefit from increased surface hardness, reducing wear from repeated use and exposure to harsh conditions.
Aerospace and Naval Defense Components
In aerospace and naval defense, liquid nitriding is applied to components like jet engine parts and submarine hulls. The process ensures these parts can withstand high pressure, temperature variations, and corrosive environments.
Advantages Over Traditional Treatments
Superior Wear Resistance
Compared to conventional surface treatments, liquid nitriding offers unmatched wear resistance, essential for the rigorous demands of military operations.
Enhanced Fatigue Strength
The process significantly increases fatigue strength, a critical factor for components subjected to cyclic stress, a common scenario in military applications.
Corrosion Resistance
Liquid nitriding imparts exceptional corrosion resistance, making it ideal for equipment used in diverse and often harsh environments.
Case Studies: Liquid Nitriding in Action
Armored Vehicle Durability
An armored vehicle manufacturer reported a 40% increase in the lifespan of nitrided components compared to untreated ones, leading to reduced maintenance costs and enhanced safety.
Firearms Efficiency
A defense contractor observed a significant reduction in barrel wear and maintenance requirements for firearms treated with liquid nitriding, improving overall operational efficiency.
Challenges and Solutions
Process Optimization
Optimizing the liquid nitriding process for specific applications in the defense industry requires precise control over temperature and treatment duration to achieve the desired surface properties.
Material Compatibility
Not all metals respond equally to liquid nitriding. Research and development are ongoing to expand the range of materials that can benefit from this process.
Conclusion
Liquid nitriding has emerged as a game-changer in the defense and military industry, offering unparalleled improvements in material performance. As metallurgical technologies continue to evolve, the potential for further enhancing military equipment and operations through advanced surface treatments like liquid nitriding is vast and promising. The future of defense material engineering, undeniably, holds exciting possibilities with liquid nitriding at the forefront.