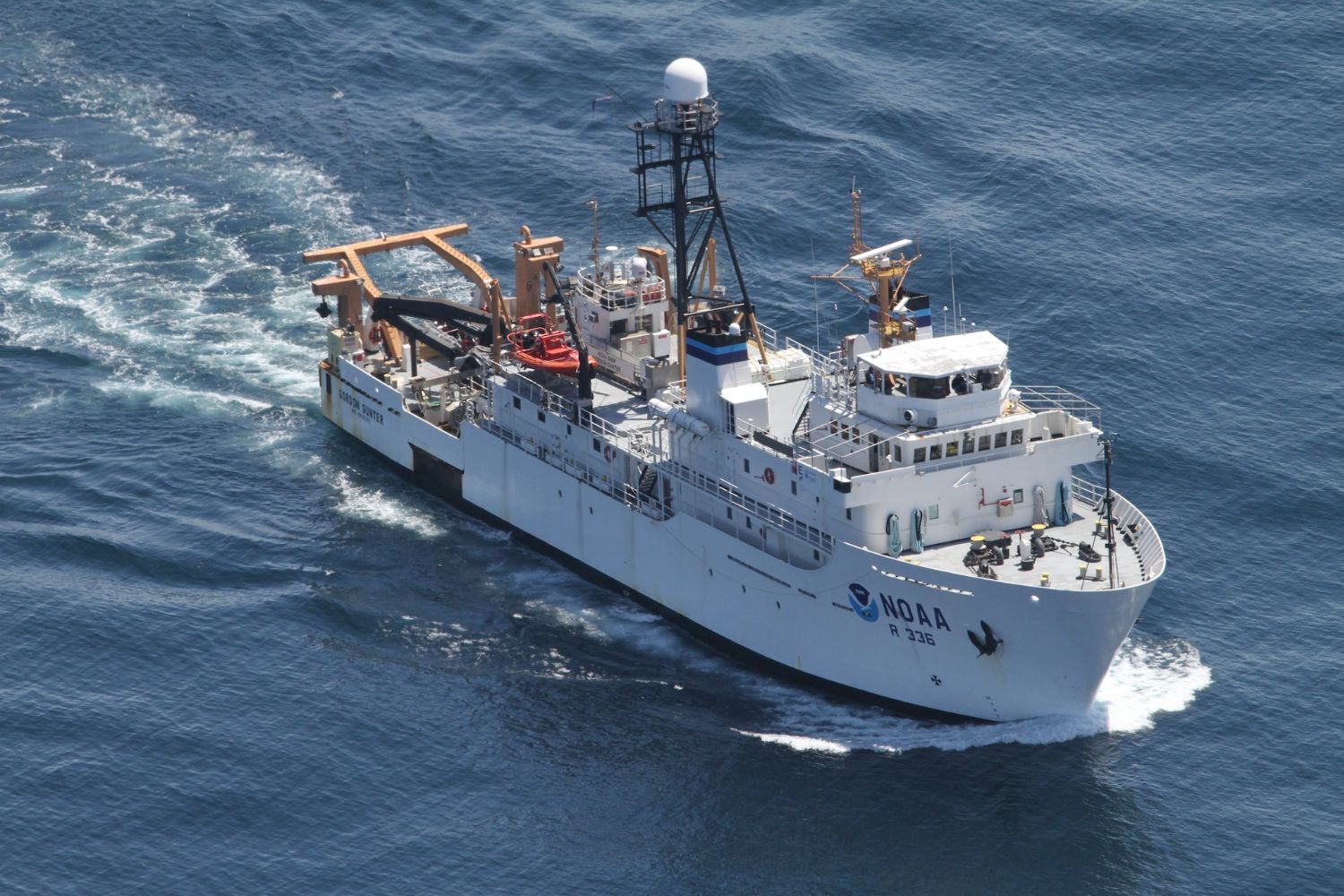
Metallurgical engineering, a field always on the cusp of new discoveries and innovations, plays a pivotal role in enhancing material properties for various industries. Among these advancements, liquid nitriding stands out, especially in its application in the marine sector. This process, renowned for its ability to significantly improve the wear and corrosion resistance of metals, becomes particularly vital in environments as challenging as the sea.
Understanding Liquid Nitriding
Before delving into its marine applications, it's essential to understand what liquid nitriding entails. This thermochemical process involves immersing metal parts in a nitrogen-rich salt bath at high temperatures. The result is a hardened surface layer, which substantially improves the material's wear and fatigue resistance, as well as its corrosion resistance – attributes crucial for marine components.
Key Benefits of Liquid Nitriding
The primary benefits of liquid nitriding include enhanced surface hardness, improved corrosion resistance, and increased fatigue strength. These improvements are particularly beneficial for metals exposed to harsh marine environments, where they are susceptible to corrosion and wear.
Marine Industry Challenges
The marine industry faces unique challenges, primarily due to the corrosive nature of saltwater and the constant wear and tear from operational stresses. Components used in ships, submarines, and offshore structures must withstand these harsh conditions while maintaining their structural integrity and performance.
Importance of Corrosion Resistance
In the marine environment, corrosion is a constant threat. Saltwater can rapidly degrade metal, leading to failures that can be catastrophic. Liquid nitriding's ability to enhance corrosion resistance is thus a critical factor in choosing materials and processes for marine applications.
Liquid Nitriding in Marine Applications
Liquid nitriding finds its place in the marine industry by extending the life of components that are regularly exposed to corrosive environments. Its applications range from small fasteners to large structural components of ships and offshore platforms.
Specific Applications in Marine
Some specific examples of liquid nitriding in marine applications include:
- Propellers and shafts that require enhanced wear resistance.
- Valves and pumps that benefit from the process's corrosion-resistant properties.
- Hull components that are continually exposed to saltwater.
Case Studies: Liquid Nitriding in Action
Several case studies highlight the effectiveness of liquid nitriding in marine applications. For instance, a shipping company reported significantly reduced wear and tear on their liquid nitrided propeller shafts, resulting in fewer maintenance requirements and longer operational life.
Long-Term Benefits and Cost Efficiency
The long-term benefits and cost-efficiency of liquid nitriding in marine applications cannot be overstated. By extending the lifespan of components, the need for frequent replacements and repairs is greatly reduced, leading to considerable cost savings over time.
Comparison with Other Surface Treatments
While there are various surface treatment options available, liquid nitriding stands out due to its unique combination of benefits. Compared to other treatments like chrome plating or paint coatings, liquid nitriding offers superior wear and corrosion resistance without compromising the material's inherent properties.
Advantages Over Alternative Methods
The advantages of liquid nitriding over alternative methods include its ability to treat complex geometries without dimensional distortions, and its environmentally friendly process, which is crucial in today's eco-conscious world.
Future of Liquid Nitriding in Marine
Looking towards the future, the application of liquid nitriding in marine engineering is poised to grow. As the industry continues to seek more durable and long-lasting materials, the demand for advanced surface treatments like liquid nitriding is expected to rise.
Innovations and Technological Advancements
Innovations in liquid nitriding, such as the development of more efficient and eco-friendly processes, are likely to further enhance its applicability and effectiveness in the marine sector.
Conclusion: A Vital Tool for Marine Durability
In conclusion, liquid nitriding emerges as a vital tool in the arsenal of marine metallurgical engineering. Its ability to significantly enhance the wear and corrosion resistance of metals makes it indispensable for the longevity and reliability of marine components. As metallurgical engineers continue to innovate, the role of liquid nitriding in marine applications will undoubtedly become more pronounced, ensuring safer and more efficient marine operations.